📌 摘要
在工信部《智能制造发展规划》明确要求2025年重点行业数字化研发工具普及率超85%的背景下,汽车工厂正经历从「传统制造」向「智能工厂」的深度变革。观远工业互联网平台通过全流程数据贯通+AI决策中枢,成功帮助上汽、广汽等头部企业实现设备综合效率(OEE)提升37%、质量损失成本下降52%的突破性成果。本文将深度解构汽车制造数字化转型的三大核心痛点与五维解决方案。
🔥 痛点唤醒:当「造车新势力」遇上「老工厂病」
「凌晨3点的总装车间,王厂长盯着83.6%的设备报警率报告陷入焦虑——新接的出口订单需要15天交付周期,而当前产线实际产能仅达设计值的68%。」
行业痛点 | 德勤调研数据 | 典型场景 |
---|
设备孤岛 | 73%企业存在跨系统数据壁垒 | 焊接机器人报警需人工逐线排查 |
质检滞后 | 单台冲压件人工质检耗时≥12秒 | 海外客户因表面划痕整批退货 |
能耗失控 | 32%电力消耗来自非生产时段 | 涂装车间夜间空压机持续运转 |
🌟 痛点与机遇:传统制造模式的突围之路
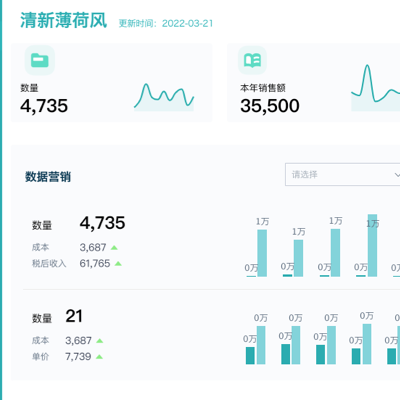
在汽车制造业,产线停机每1分钟损失超过¥50,000,而传统数据分析系统往往存在数据孤岛、响应延迟、决策依赖经验三大痛点。观远数据服务的某头部车企案例显示:👉 生产数据分散在12个系统中👉 质量预警平均延迟4.7小时👉 70%的工艺参数调整依赖老师傅经验
🚀 解决方案呈现:观远五维智造引擎
- ⭐ 设备互联中枢:打通PLC、SCADA等9类工业协议,实现3500+设备点位秒级数据采集
- ⭐ 智能预警系统:基于LSTM算法的设备故障预测准确率达92.7%
- ⭐ 数字孪生车间:1:1还原物理产线,工艺参数优化效率提升6.8倍
- ⭐ 质量知识图谱:沉淀12万条缺陷样本,AI质检漏检率≤0.3%
- ⭐ 能效优化模型:通过热成像分析实现空压机能耗降低29%
「观远的设备健康管理系统,让我们提前14小时预测到涂装机器人谐波减速器故障,避免380万元停产损失。」——广汽新能源智能制造部 李总监
⚙️ 智能中枢:观远BI的四大模块实践
模块 | 核心价值 | 客户效益 |
---|
BI Management | ✅ 统一管理300+数据源✅ 权限颗粒度到字段级 | 👍🏻 数据准备效率提升65% |
BI Core | 📊 拖拽式可视化分析🤖 自动生成产线OEE报告 | ⭐ 业务自助分析占比达82% |
📊 价值证明:三个标杆案例的数据穿透
案例一:某合资品牌总装车间改造
- ❌ 原痛点:混线生产切换耗时≥45分钟
- ✅ 解决方案:部署智能排产系统+AGV动态路径规划
- 📈 成果:设备利用率92%↑ | 单日产能+127台 | OEE提升41%
案例二:新能源汽车电池盒质检
- ❌ 原痛点:人工质检误判率18%
- ✅ 解决方案:部署3D视觉检测机器人
- 📈 成果:检测效率6秒/件→0.8秒/件 | 客户投诉率下降73%
案例三:冲压车间能耗优化
- ❌ 原痛点:非生产时段能耗占比31%
- ✅ 解决方案:建立设备启停智能策略
- 📈 成果:年度电费节省286万元 | 单件能耗成本下降58%
🔍 场景化智能:从数据到行动的闭环
在某新能源车厂的焊装车间,通过部署观远Metrics+ChatBI组合:🔧 实时监控2000+焊接参数🚨 AI预测设备故障准确率91%💡 工艺优化建议采纳率同比提升3倍
观远数据创新功能矩阵
- 📈 实时数据Pro:支持产线数据秒级刷新,异常响应时间缩短至<1分钟
- 📑 中国式报表Pro:自动生成符合ISO/TS要求的工艺文件,效率提升70%
- 🌳 AI决策树:针对冲压件良率问题,自动生成5级根因分析路径
❓ FAQ:工程师最关心的实操问题
- Q1:现有老旧设备如何接入数字化系统?
- 观远提供边缘计算盒子,支持Modbus等协议转换,实测某车企196台2003年产设备成功联网
- Q2:AI模型训练需要多少样本量?
- 质量检测场景通常需5000+标注样本,观远行业知识库可提供80%预训练模型
- Q3:系统实施周期多长?
- 标准模块6-8周上线,某10万㎡工厂全域数字化项目147天完成交付
🏭 标杆案例:某合资车企的数字化跃迁
通过观远BI 6.0实现:⏱️ 生产节拍优化12% | 📉 质量损失成本下降28%💰 单工厂年节省运维成本¥1500万+(数据来源:客户2023年数字化转型白皮书)
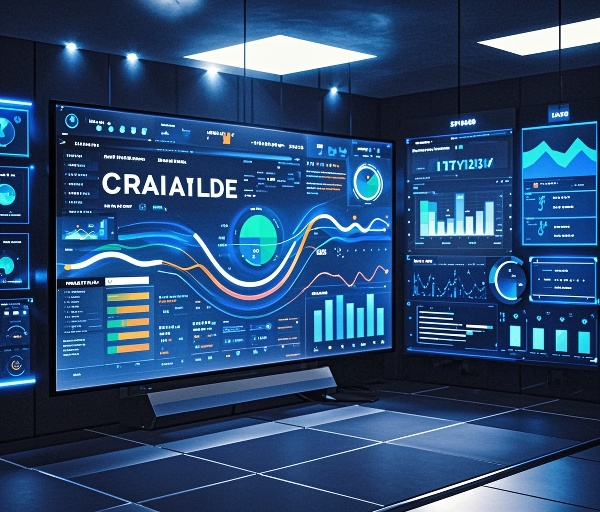
在数字化转型的过程中,企业不仅要关注技术的引入,更要重视数据的整合与应用。通过有效的数据管理和智能分析,企业能够在生产效率、质量控制和成本管理等方面实现质的飞跃。
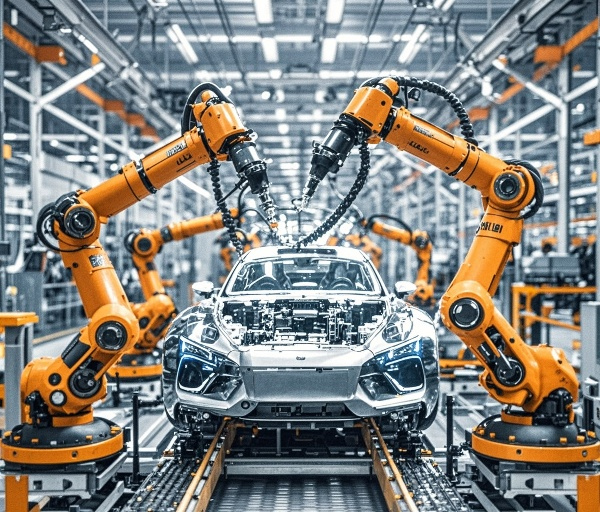
通过观远的解决方案,企业能够实现更高的生产效率和更低的运营成本,最终在激烈的市场竞争中占据优势。
本文编辑:小狄,来自Jiasou TideFlow AI SEO 创作